Last Mile Delivery Optimization, Route Optimization
How Delivery Logistics Software Helps Businesses Winter-Proof Their Logistics Operations
Mar 9, 2021
12 mins read

Few of the severe and defining issues that have cropped up with global warming are the unprecedented and inevitable climate events like the one in Texas. It has become impossible to predict events such as winter storms, hurricanes, polar vortices and wildfires. The need of the hour is efficient contingency plans.
Trucking companies have more pressure to keep rolling on schedule and cannot wait for the uneven weather to stop. They face power outages, traffic diversions, road closures, long delays at overwhelmed terminals due to uneven weather conditions.
As winter storms hit North America during this period, many logistics companies prepare their fleet checklists to enable smoother operations. Businesses involved in logistics always sort out how they can operate their supply chains without interruptions in winter or extreme temperature swings.
What is vehicle downtime?
There is no specific industry definition for downtime. Vehicle downtime is the time in which a vehicle is pulled out of the service until the driver resumes the work. It is the period during which a vehicle is not operating or is unavailable. Repair time should not be confused with downtime.
Types of vehicle downtime
Vehicle downtimes occur due to planned reasons or unplanned reasons. Downtimes that occur due to planned reasons are called planned downtime. Downtimes that occur due to unplanned reasons are called unplanned downtime.
Unplanned downtime
Unplanned downtime is the time vehicles spend off the road because of incidents like collisions, breakdowns, delays in service/maintenance, or repair schedules. They attract less visible costs or soft costs on the budget like:
- Cost of replacing a vehicle and ruined goods
- Paying drivers for unscheduled stops
- Inability to deliver goods On-Time In-Full
- Idle staff hours
- Temporary vehicle repairs
- Extra manpower costs to move cargo to another vehicle
- Lost opportunities from failed and missed deliveries
Planned downtime
Planned downtime is the time period during which activity in a company slows down due to the implementation of new technology, refresher training, vehicle inspections and scheduled servicing.
Planned downtimes have visible costs or hard costs such as regular maintenance checks to get their vehicles back on road. These costs vary based on the repair costs, labor costs, age of the vehicle among other things.
Ex: Planned downtime costs include towing charges, lost revenue, temporary rental, and employee overtime.
Vehicle downtime events are unavoidable in the real-world. Actually, there are costs involved to keep vehicles running smoothly and efficiently. When there is unplanned downtime, these costs are higher than expected. Hence, planned downtimes are easier to manage compared to unplanned downtime.
Impact of logistics breakdown on supply chain during the winter season

Vehicles face major logistical breakdown challenges during the winter compared to other seasons. Before trying to solve vehicle downtime, it is necessary to understand the effects of unplanned downtimes on supply chains during winters. Unplanned downtimes, especially during winters, have a huge impact on the operational capabilities of the supply chain.
Capacity
Unplanned winter breakdowns push fleet managers to focus more on their trucking capacity. They result in poor delivery performance, reduced battery power, and rough idling.
Unplanned vehicle downtimes during winter make accelerating, tuning, and braking extremely risky leading to a host of visibility issues. They may even lead to equipment failures of vehicles for which the businesses should be prepared. It will be challenging to proceed with deliveries if fleets do not have parts or tools to replace equipment failures in vehicles.
When trucking capacity is not maintained, it leads to some vehicle stoppage in midway. Especially during winters, it becomes difficult to reallocate alternative vehicles when the majority of the trucks are off the roads.
Road Closures
Road closures are one of the biggest hindrances caused by cold weather when businesses set out to deliver products. Beyond affecting traffic speed, they result in increased travel time and dangerous driving conditions that hold a higher risk of accidents.
During weather storms, drivers lose control over their vehicles as they ride over bridges or ramps. Some issues like sudden power outages, disconnected internet, or map irregularities driven by uneven weather conditions reduce the visibility of delivery operations.
Businesses should check if the loading bays, car parks, or walkways are safe for driving and parking. They must invest in winter tyres to attain a better grip and reduced stopping distances. These small preparations and preventive measures keep their supply chains resilient.
Stockouts
As people prepare for potential disasters during winters like storms, they purchase more goods from nearby outlets. Due to this sudden purchase spike, the store shelves get emptied quickly following power outages.
During these surviving conditions, people oscillate towards online shopping. As the majority of customers begin to rely on deliveries, there is an increased pressure for fleet drivers to work on tight delivery schedules.
Lead times
When people order products online during the winter seasons, lead times become quite unpredictable. As the parcel volumes keep piling up, it becomes difficult to schedule deliveries and plan ETAs.
Unplanned winter breakdowns reduce on-time deliveries and customers may not be able to receive the product when they want. The increase in lead time coupled with the unavailability of vehicles causes clashing of delivery tasks. It adds more difficulty to allocate deliveries and plan optimal routes.
Rejected loads
Truckers hate rejected loads especially when they are distributing perishable products. The receiver won’t accept the portion or entirety of what fleet drivers have been carrying if they strictly do not follow delivery deadlines. It is challenging to find the alternative receiver for products in the middle of the crisis, thereby leading to idling away precious time.
Limited vehicle capacity and a lack of backup plan during these winter breakdowns maximize rejected loads.
Delayed shipments
Delivery businesses find it challenging to deliver goods to areas affected with winter storms, cyclones, power outages or hurricanes etc. These unusual weather conditions can likely trigger logistics breakdowns that result in delivery delays.
With limited vehicle capacity and driver shortage during these uncertain situations, fleet managers cannot pressurize drivers to ride in haste for quick deliveries.
Rising costs
Logistics breakdowns during winters lead to a spike in costs through ripple effects of delayed deliveries, increased demand, and reduced supply.
Costs are bound to increase when businesses undertake logistics operations during the winter months. But all that is under the control of the firm is to reduce the planned breakdowns and take preventive measures for unplanned breakdowns.
How delivery logistics software helps to winter-proof your logistics operations

It is necessary to train fleet managers and drivers to handle adverse weather conditions. Beyond training, it is necessary to keep a tool like delivery logistics software that tracks all delivery constraints and suggests solutions for them.
Plan your deliveries early
During unusual weather conditions, some roads may be closed or are too difficult to navigate. Information on real-time road conditions is necessary in order to plan routes during winter. This information helps drivers to ride with more visibility and avoid sporadic driving.
Planning deliveries early helps businesses gauge their vehicle limitations. It helps them to calculate their driving speed and pre-arrange safe parking locations. It enables them to judge and make decisions if they want to continue with travel or stop in a parking spot till storms abate.
Delivery logistics software helps businesses plan alternate safe stops in case conditions get too bad in other places. It enables them to solve issues facing Hours of Service (HOS) before making it to a safe resting stop. It also helps them analyze the road conditions and vehicle capacity and plan routes accordingly.
Facilitate effective internal and external communication
Communication is the most essential tool to manage the logistics breakdowns of winters. It is necessary to maintain both internal and external communication because an irregularity in either of these can make delivery decisions tougher.
The fleet drivers or fleet managers have the responsibility to keep their upper management informed of additional costs due to weather-related conditions. Also, the business that undertakes the logistics operations has the responsibility to communicate to their customers when it fails to meet on-time delivery promises.
Delivery logistics software tracks real-time information of the on-ground conditions and makes it visible through an accessible dashboard. It enables fleet managers or the upper management to take a call on risky delivery decisions when weather hinders delivery operations. It also keeps the customers in the loop and informs them about the delivery delays through timely notifications and alerts.
Flexibility in deliveries
Winter logistics breakdowns test the flexibility of carriers when it comes to last-mile delivery. With more flexibility, businesses can strategize and prioritize deliveries without burdening drivers. It helps drivers accommodate additional deliveries with more speed and control.
The use of delivery logistics software reduces fulfillment time. It helps fleet managers to fulfill orders from multiple locations when there are any unintended breakdowns. It enables them to redirect orders in real-time through alternative pick-up destinations, nearby available drivers, and vehicle capacity. This provides enhanced flexibility in assigning drivers to different delivery windows based on safety requirements.
Delivery logistics software keeps customers informed of the latest updates in the delivery through timely notifications. When there are any weather issues, it enables customers to change delivery location, time or provide instructions on where to leave a package. This provides a greater sense of control for customers to schedule their delivery.
Customize reports to the winter-season
Effectively managing weather-related issues requires different information and analyses. Historical data helps fleet managers to act on the latest weather trends and solve associated problems in different areas of delivery operations. It helps a delivery company to smartly counter unplanned winter breakdowns in areas that are vulnerable to extreme weather.
Delivery logistics software monitors real-time reports on weather conditions in different delivery zones. It dynamically updates the changeable nature of patterns and enables them to circulate frequently. It provides a micro and macro view of the delivery metrics in safe and danger zones.
These detailed insights on weather issues in different areas help fleet managers to shift high-impact loads from danger zones.
Develop effective rerouting ability
Planning optimal routes in the midst of unlikely weather issues is a daunting task. If there are extreme weather issues in some delivery areas, businesses limit their delivery tasks till conditions resume to normal. Some businesses will analyze the severity of weather conditions at the danger zone and select safer areas within them to deliver the products.
Delivery logistics solution helps fleet drivers when there are any deviations in already planned routes. It dynamically reroutes optimal delivery routes in seconds when there are last-minute delivery changes due to weather issues. It enables drivers to improve their First Attempt Delivery Rates (FADR), without burdening them with tight delivery time windows.
A delivery logistics software helps fleet managers to quickly reassign deliveries to nearby drivers when there is a weather-driven vehicle stoppage. This reduces the number of missed deliveries and failed deliveries, thereby enhancing customer experience.
Ensure proper vehicle selection
Vehicle capacity is the major factor in planning routes for last-mile logistics during winters. Sending vehicles that don’t suit extreme weather conditions to the danger zone is risky. Hence, it is necessary to run a complete vehicle capacity check before planning delivery schedules for drivers.
Delivery logistics software crucially factors vehicle capacity and driver skill set while planning delivery schedules. It comes in handy when assigning vehicles based on different road conditions and weather issues. It ensures that fleet managers do not burden the delivery schedules with unnecessary loads, thereby making the delivery processes smooth.
Maintain scheduled vehicle maintenance effectively
Improper vehicle conditions add more burden to logistical breakdowns during winter. Regular vehicle maintenance checks are essential to counter extreme weather conditions. They maximize the resilience of a fleet to unplanned breakdowns and reduce idling time.
Delays in scheduled maintenance cause unscheduled vehicle downtime. A tool like delivery logistics software comes in handy when fleet managers have to make strict vehicle maintenance checks. It helps them proactively monitor the length of time vehicles spend in garages.
Delivery logistics software provides crucial vehicle usage information like fuel consumption, idling, unscheduled stoppages, etc. These insights help fleet managers to have backup plans when a vehicle is off the road. These metrics help them keep a check on fuel expenses, idling costs, or empty miles that actively contribute to last-mile delivery costs.
Delivery logistics solution helps logistics managers track and analyze the vehicle stoppages due to extreme weather issues. This helps them to set up alternative vehicle arrangements nearby, new pickup spots, etc reducing the time vehicles spend on the road. It minimizes the chances of any accidents and helps them keep a check on maintenance expenses.
Conclusion
Weather-proofing logistics operations is a comprehensive effort that involves the right equipment, training, and preventive maintenance. An extensively weatherproofed operation improves fleet assets and capabilities to attract and retain customers. A delivery logistics software is the best tool to monitor and improve fleet capabilities to handle these weather issues.
Locus’ Delivery logistics software helps fleet managers to set effective delivery schedules during winter. It enables them to assign deliveries based on vehicle capacity, weather conditions, driver skill sets, road closures, and so on. It enables logistics businesses to manage efficiency standards and minimize logistics breakdowns without compromising safety standards.
Related Tags:
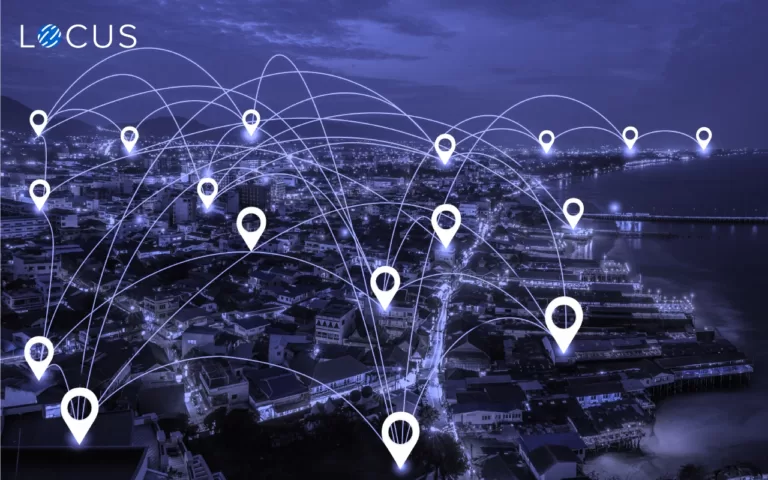
Tech and Product
Liberalization of Geospatial Data and Mapping Policies Could Unlock New Doors for India’s Logistics Tech Industry
India’s Ministry of Science and Technology has announced changes to the country’s mapping and geospatial data laws, liberalizing regulations on geospatial information, making it freely available for innovation and IT companies across the country. New guidelines have been issued for acquiring and producing geospatial data and geospatial data services, including maps. Indian citizens, corporations, and […]
Read more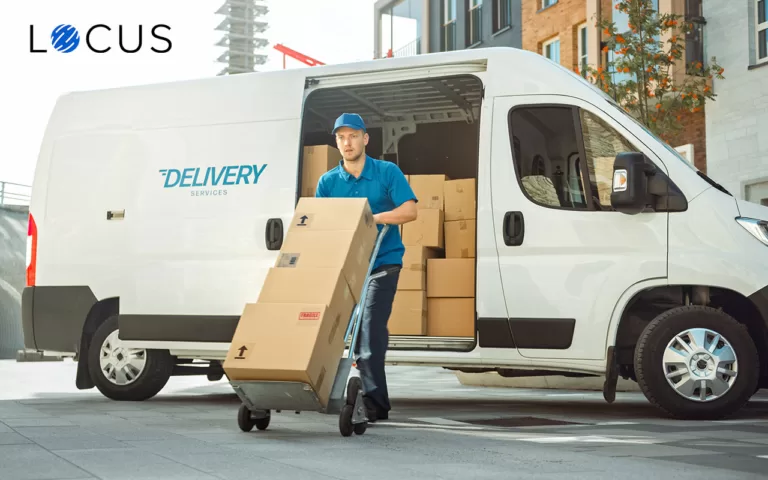
Retail & CPG
How to Optimize Permanent Journey Planning (PJP) in FMCG and Retail Supply Chains
Revenue is driven by a number of different factors in retail and FMCG markets — constantly evolving customer expectations, rising market competition, omnichannel trends, location demographics, and the effectiveness of supply chain elements, especially timely and effective distribution of goods to retail outlets from where the end customer buys the products. Typically, this is how […]
Read moreMOST POPULAR
EDITOR’S PICKS
SUBSCRIBE TO OUR NEWSLETTER
Stay up to date with the latest marketing, sales, and service tips and news
How Delivery Logistics Software Helps Businesses Winter-Proof Their Logistics Operations