E-Commerce, Last Mile Delivery Optimization, Retail & CPG
Last Mile Delivery Costs: Bringing Order to Chaos
Apr 1, 2020
14 mins read
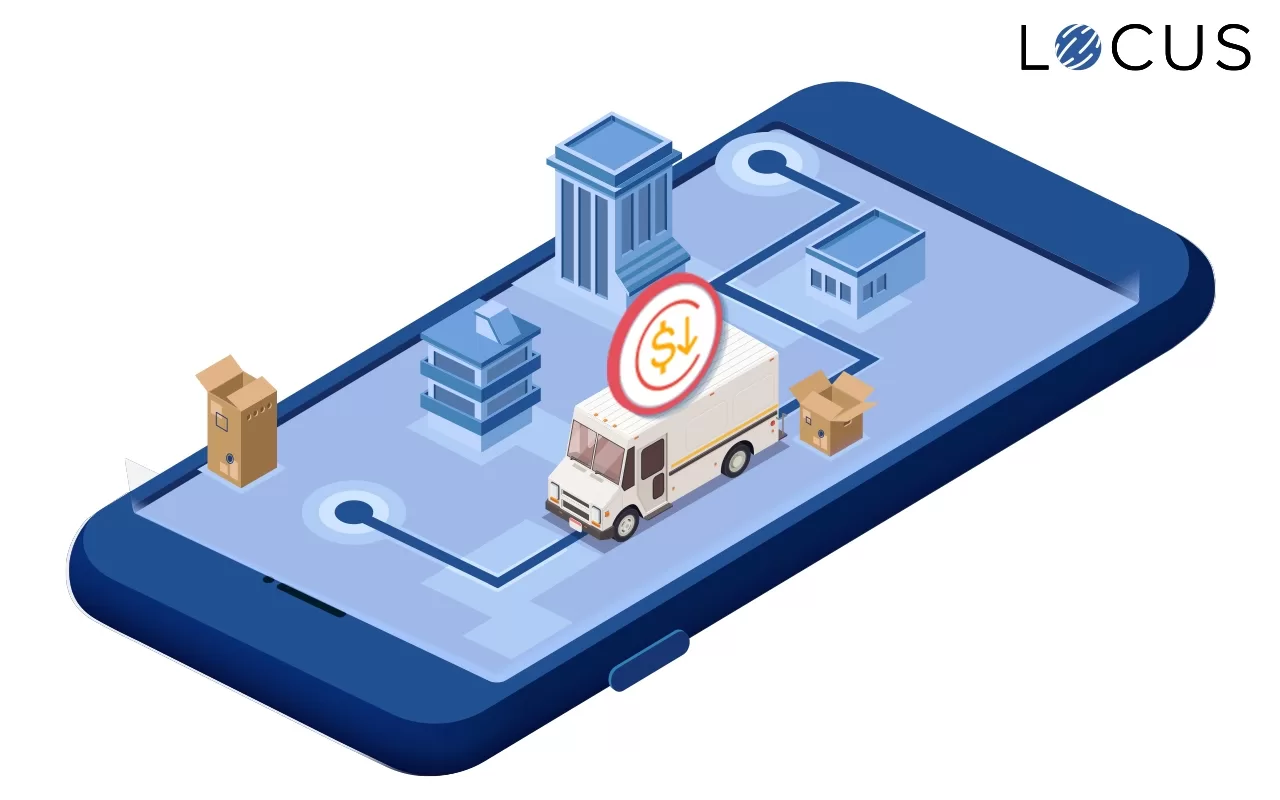
Last-mile delivery costs consume over two-fifths of overall logistics costs.- Frost and Sullivan, 2018
It is no secret that customer expectations are really high these days. Naturally, the costs associated with meeting such expectations, especially on the delivery front are also increasing. The primary challenge that logistics providers face is rising last-mile carrier delivery costs. Hence, businesses must take proactive measures to improve the efficiency of their last-mile delivery services.
The retailers or logistics providers should not shift the burden of costs on the consumers. Passing on the cost burden makes consumers unhappy and leads to churn. Thus, businesses should enhance their delivery services without hurting their profit margins.
What do you mean by last mile delivery costs in logistics?
Last-mile delivery deals with the movement of goods from the retailers’ transportation hub to the final delivery destination.
E-commerce businesses are trying to build experimental supply chain models and new technologies. They try to delight customers with the best delivery experience, by trying to cut costs. The biggest challenge that they face is the delivery costs of last mile.
The expenses incurred in the last mile of the shipping journey are called last-mile delivery costs.
What are the costs involved in Last mile delivery?
Logistics companies are experiencing a rise in last-mile delivery costs because of rising delivery complexities. Here are the costs that are involved in last-mile delivery.

Fuel costs
There is a need to carefully scrutinize the fuel costs in the last-mile. This is because fuel prices are volatile. Its irregular fluctuations make it a concern for the last-mile operations of companies.
Fuel cost is a good starting point to understand the efficiency of last-mile delivery. Its share in total operational cost also determines the overall cost of last-mile deliveries.
Fuel costs share 25 percent of total operational costs of a truck- American Transportation Research Institute, 2019
Journeys to sparsely populated areas can add to your fuel costs. This is because you have to travel long distances between stops in rural delivery zones. But it is not the case with urban areas.
In urban areas, you may have more delivery stops before you complete the delivery schedule. Hence, idling eats up fuel costs in densely populated areas. Executing same-day deliveries in congested urban areas increases fuel costs further.
Why should you reduce fuel costs in the final-mile delivery?
- Analyzing fuel consumptions helps in understanding fuel wastage on service times, routes, and stops
- Enhances your route planning and strengthens your efficiency along the route
- Balance your capacity utilization costs
Labor costs
Presently, the logistics industry faces a severe shortage of qualified drivers.
There is a worsening driver shortage in the US logistics industry. The primary area of concern for the logistics industry in the US is the lack of professional truck drivers.
71% of freight tonnage moved in the US goes on trucks, and the driver shortage could reach 174,000 by 2024. -Bob Costello, American Trucking Association.
The wages of truck drivers is seeing a sharp rise in the US because of the shortage of drivers and added responsibilities.
Wages of truck drivers share 33% of the total operational costs of a delivery truck.- American Transportation Research Institute, An analysis of Operational costs of trucking, 2019
Idling costs
Idling has become another challenge for logistics companies undertaking deliveries in urban areas. A part of inefficiency in fuel consumption can be attributed to idling. It leads to the wear and tear of a vehicle and hence to frequent maintenance issues.
An hour of idling results in gallons of gas lost. Even ten seconds of idling leads to a waste of more fuel than restarting the engine. Reducing unnecessary idling can save fuel and maintenance costs.
One hour of idling per day causes an equivalent of 64,000 miles in engine wear. – American Trucking Association.
Reverse logistics costs
Reverse logistics costs are incurred when customers decide to return the products they have received. The customers repackage a product and then return it to the shipping company. From the shipping company, the products move to the warehouse or distribution center.
Returns result in enormous costs for companies accepting it. But it is a crucial component of online businesses as it builds trust among consumers.
89% of online shoppers mentioned that a return policy controlled their decision to order a product from a company- Bizrate survey, Harris Williams & Co, 2016.
Hence, managing reverse logistics costs is a crucial aspect for logistics companies. There are two costs involved when a consumer returns a product. They are refund costs and replacement costs.
Refund costs
Consumers want goods to be delivered on their preferred time windows. Also, they are demanding quicker deliveries. If there are failed or delayed deliveries, consumers expect a percentage of that amount to be refunded. Sometimes customers don’t want to replace the product. They just want to get refunds for their returns.
E-commerce companies are bearing the cost of free shipping, failed deliveries, and late deliveries with refund costs. Hence, these refund costs add more burden on the logistics.
Replacement costs
Consider this, Robert purchased an L-sized shirt but found out that it was a tad bit bigger for him and hence decided to return the shirt and replace it with an M-size. Here the logistics company bears not only the return costs but also the replacement cost.
Replacement cost is incurred when consumers replace a product that they have ordered. When consumers return a product, there are reverse logistics costs involved. After the replacement is applied, there is a regular last-mile logistics cost involved. Because you have to deliver the replaced products to the consumer again.
Thus, a company incurs regular last-mile logistics cost twice and a reverse logistics cost once. But today’s consumers want zero or low-cost shipping for reverse mile logistics, and regular last-mile logistics. This demand from consumers has multiplied cost burdens on the last-mile delivery.
Environmental costs and Congestion costs
Delivery vehicles have become a major contributor to air pollution in urban areas. They can create traffic jams on the busy streets of major cities. Not managing the volume of deliveries leads to unsustainable levels of carbon emissions.
Delivery vehicles in the UK produce 23 times the level of toxins than permitted by UK law.- Tests from Sunday times, 2017.
The rising congestion and emissions from E-commerce delivery are putting a heavy burden on city traffic patterns. With multiplying customer demand, this burden is going to increase further. Hence, these last-mile delivery emissions are going to increase.
Urban last-mile delivery emissions are going to increase more than 30% in 100 cities globally by 2030.- World Economic Forum, 2020, The future of the last-mile ecosystem.
Many urban local bodies and governments are collecting hefty fines from delivery vehicles. These fines multiply last-mile delivery costs for logistics businesses.
Maintenance costs
Imagine that you have got deliveries scheduled for the day and a truck suddenly has some maintenance issue. It will certainly cost your deliveries scheduled for the day. Indirectly, it delays deliveries and creates a bad delivery experience for consumers.
Maintenance costs determine the active operation and efficiency of fleets. Traveling long distances or consistent idling can lead to sudden wear and tear of vehicles. An increase in maintenance costs leads to an increase in overall last-mile delivery costs.
Repair and maintenance costs rose to 17.1 cents per mile from 16.7 cents because of an increase in the purchase of trucks and trailers.- American Transport Research Institute, 2018.
Logistics companies aim to minimize maintenance costs without compromising vehicle performance. Reducing maintenance costs prevents the delivery vehicles from unnecessary downtimes.
Storage costs
Logistics companies involved in the last-mile delivery do incur storage costs, especially those involved in pharmaceuticals, food, and groceries. Fleet drivers want delivery vehicles with improved facilities.
33% of logistics companies are investing in new vehicles and improved facilities to attract new drivers.- FTA Logistics Industry Survey, 2018-2019.
Some companies in last-mile delivery do incur capacity utilization costs. Capacity utilization mentions the empty space that a fleet driver or manager wastes on a truck. More the empty space, higher are the fuel and labor costs.
What does poor capacity utilization mean?
- Poor loading procedures
- Improper consolidation of routes
- Inefficiency in organizing shipments
The proportion of used space in a delivery vehicle determines last-mile delivery efficiency. If you want to optimize fuel consumption and plan the best routes, then utilize close to 100% of the space of delivery vehicles. If the proportion of used space in a delivery vehicle is less than 80%, then fleet managers should re-evaluate their efficiencies.
Check Out: The Definitive Guide to Route Planning
Why are last mile delivery costs increasing?

Last-mile delivery costs are eating up the profit margins of E-commerce companies and retailers today.
Companies absorbing the last-mile delivery costs are showing a potential decline in profit by 26% in 3 years.- Last-mile delivery challenge, Capgemini Research.
Identifying and reducing the drivers of last-mile delivery costs can enhance the profit margins. Here are some factors that increases delivery costs:
Bearing free shipping costs
Consumers are expecting quick deliveries with free or low shipping costs. Logistics companies are finding it difficult to manage on-time deliveries at zero shipping costs. These free shipping costs add more pressure on logistics companies.
Increasing occurrence of failed deliveries
Failed deliveries increase your last-mile delivery costs. It impacts the distance travelled, emissions, and costs. Some goods can be easily handled, but some goods require specialized care, handling, and security, for example, goods that require refrigeration. It is therefore costlier if a failed delivery were to occur in these sorts of shipments.
Failed or late deliveries cost retailers almost $69, adding up 4.7 days of fulfillment and returns.-Convey, What shoppers want from last-mile, how to save retail
Poor routing plans due to low density
Lower population density leads to additional costs and increased transit times. This creates difficulty in executing profitable and efficient routing plans for last-mile deliveries.
Products requiring temperature control
Some products require temperature control which adds to additional storage and transportation costs. These temperature-sensitive products push up storage, fuel and driver costs.
Unpredictability in scheduled deliveries
The sudden change of routes, route maintenance, or traffic congestion adds unpredictability in last-mile deliveries. This unpredictability can lead to an increase in delivery delays thereby making your last-mile logistics operations costlier.
Is it essential to reduce last-mile delivery costs for vehicles?

Last-mile delivery costs incur 53% of shipping costs in the logistics supply chain. Final-mile Delivery markets in USA, 2020-2025, Mordor intelligence.
Last-mile industry occupies a large portion of costs in the entire shipping process. Reducing last-mile delivery costs helps adapt to shifting consumer demands and maintain a healthy profit margin.
The increase in the volume of last-mile orders has made it challenging for logistics companies in controlling costs and sustain delivery efficiency.
25% of logistics companies mention that maintaining delivery efficiency is their biggest challenge.- Eye For Transport, EFT, 2018.
Here are some reasons why companies should focus in cutting down last-mile delivery costs:
The face of the customer service
A company interacts with its customers through last mile tracking and the company fulfills its promises. Increasing last-mile delivery costs leads to failure in fulfilling the promise of on-time deliveries to their customers. If you provide a poor delivery service, it results in an angry tweet and a lost customer.
Most expensive stage of logistics
The infrastructure requirement of last-mile delivery makes it quite costlier. Last-mile technology companies pay for IT, backend systems, delivery agents, depots, and vehicle fleet’s wages. Failed deliveries is an added burden.
Logistics companies have to manage multiple delivery complexities in last mile logistics. Even a small glitch can lead to huge costs.
Managing evolving customer expectations
Retailers are facing greater pressure to deliver more couriers or parcels at a lower cost. Customers expect faster deliveries and increased control over the delivery experience. Reducing the last-mile delivery costs determines your ability to offer faster, flexible, and free deliveries.
How to reduce delivery costs of last-mile?

The growth of E-commerce has led to an exponential increase in the number of deliveries. It has multiplied complexity and delivery inefficiencies.
The complexity in the last-mile delivery differs based on its distance and drop size. It is evident in the drop points in rural and urban areas. Rural areas have fewer drop locations, and long distances travelled and urban areas have multiple drop locations with constant traffic delays.
Here are some ways companies can reduce last-mile delivery costs:
Execute order batching
With rising on-demand deliveries, logistics companies won’t find time to execute efficient batching. The logistics companies should handle a higher number of Stock Keeping Units, and for that, they require automated order fulfillment.
Retailers create batches for orders in an automated fulfillment system. The intelligent algorithms in the system group the orders in the same delivery window, the same location with the same driver. With this setup, on-time deliveries are possible with a limited number of drivers, thereby reducing the last-mile delivery costs.
Auto-dispatch technology ensures that you send the right driver to the right place at the right time. It helps logistics companies to adjust task limits so that you don’t assign too many deliveries to one driver. This technology saves time and labor costs in last-mile delivery.
Effective route planning
Even if your drivers know the local areas and routes, they face unpredictable delivery constraints. These constraints include traffic congestion, change in weather conditions, natural calamities or construction closures. All these challenges make drivers inefficient in planning optimal routes.
Manual routing makes your deliveries harder. Route planning in the last-mile cannot be accomplished with pen and paper. It wastes hours in designing route plans causing delayed and failed deliveries.
The best way to counter route inefficiencies is by using route planning software. Route planning solutions create optimal route plans based on real-time traffic, Estimated Time of Arrival, local knowledge of the driver, and other criteria.
Utilizing automated dispatching and routing increases revenue and logistics companies can expand their delivery range with the same number of vehicles. It also reduces delivery time, idling time, and fuel consumption.
Invest in visibility
Visibility tools and customer-facing communication tools can reduce last-mile delivery costs.
Real-time visibility software helps reduce failed deliveries. Reducing failed deliveries leads to a reduction in last-mile logistics delivery costs.
Real-time visibility tool connects driver and customer experience. It helps consumers prioritize deliveries like delivery options and delivery costs. It also maintains the privacy of communication.
Logistics companies and consumers demand greater visibility into last-mile delivery. Utilizing Electronic Proof of Delivery can fulfill this very easily. It provides insights into when drivers deliver packages, who signs it, and where they are dropped.
Create flexible delivery options
Consumers may have different requirements of speed, convenience, and price.
Providing multiple delivery options and convenient time slots reduces shipping costs and repeat deliveries thereby cutting down overall last-mile delivery costs.
Obtain real-time data to improve efficiency
Real-time data is an asset for logistics companies. Analyzing data lets, you know what is happening in the last-mile delivery. It helps you take necessary measures to eliminate delivery inefficiencies.
Here is a list of data companies can track to reduce delivery inefficiencies
- Number of tasks completed
- Distance covered
- Average time per task
- Idle time
- Successful vs. failed deliveries
- Repeat deliveries
- Missed deliveries
- Delayed deliveries
- Driver performance analysis
- Traffic
Analyzing and predicting trends based on this data can improve efficiency and reduce costs considerably.
How can i reduce my last mile delivery charges with Locus?
Logistics Companies are striving to strike the right balance between customers’ delivery expectations and profit. Technology makes it possible to keep last-mile deliveries cost-efficient, transparent, and consistent.
With Locus’ last-mile route planning software, you can automatically assign drivers and plan optimal routes for deliveries.
Locus’ automated shipment sorting allocates a rider to a delivery zone. It intelligently clusters deliveries for different delivery zones, thereby saving time and costs.

Related Tags:
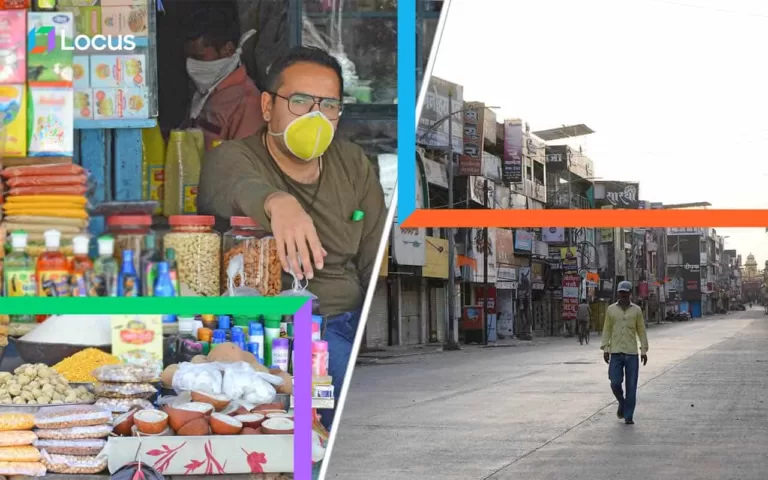
News
How India is Dealing With Essential Deliveries Amidst an Unprecedented Lockdown
India's lockdown has disrupted deliveries of e-commerce and e-grocery firms. How is India dealing with essential deliveries amidst a lockdown? Know More!
Read more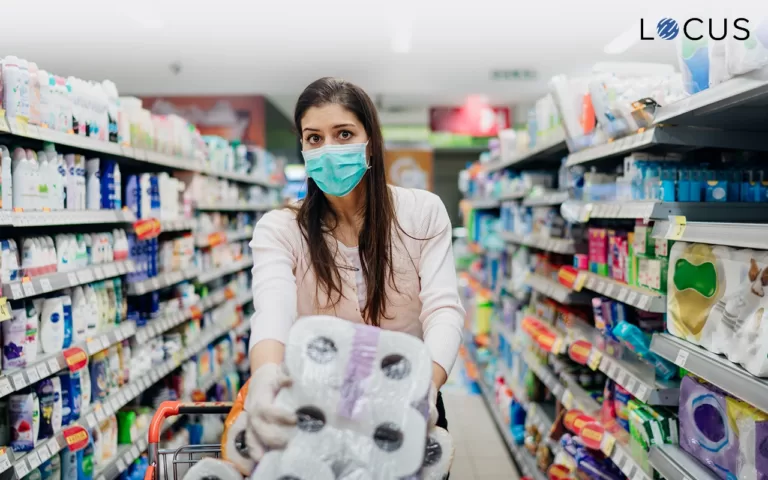
E-Commerce
The impact of Panic Buying on the Retail Supply Chain
What started as a viral flu in China’s Wuhan a couple of months ago is now a global pandemic that is affecting millions across the globe. COVID-19 has spread to more than 199 countries and territories. The United States, Italy, and Spain are experiencing the most widespread outbreaks outside of China. As of 1st April, […]
Read moreMOST POPULAR
EDITOR’S PICKS
SUBSCRIBE TO OUR NEWSLETTER
Stay up to date with the latest marketing, sales, and service tips and news
Last Mile Delivery Costs: Bringing Order to Chaos