E-Commerce, Last Mile Delivery Optimization, Supply Chain Optimization
Reverse Logistics : Forward Thinking Pays Big Dividends
Sep 26, 2016
6 mins read

“The line between disorder and order lies in logistics” — Sun Tzu, The Art of War
Over the past few years, the global logistics industry has witnessed an increased interest in product returns, recovery, exchange and redistribution. Stats validate that 8 to 9 percent of goods purchased at brick and mortar stores and 25 to 30 percent of e-retail orders are often returned.
Forward logistics, traditionally, has been considered key to governing sales and profit margins while retailers handled returns considering it a service for increasing customer loyalty. However, in the recent times, handling reverse logistics has become more of a conscious strategic consideration when planning supply chain networks. Technology has been a boon in facilitating increase in deliveries and reducing transport time & cost.
Reverse Logistics is the process of moving goods from their final destination for the purpose of handling exchanges, returns, refunds, or proper disposal. Broadly, when a customer chooses to return a product, the cog wheels move and a reverse logistics chain is activated.
So why is reverse logistics so important?
The impact of an online retail customer’s return experience can be summed up as below.
- 85% of customers WILL NOT shop with you again if the return process is not convenient
- 95% of customers WILL shop with you again if the returns process is convenient.
— Harris Interactive study
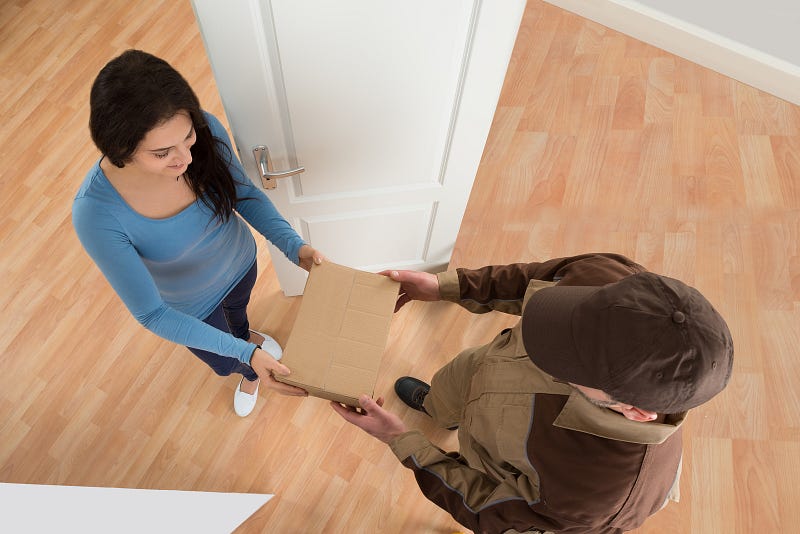
Studies tell us that 1 to 2 percent of sales returns’ can be handled in the warehouse and returned to the vendor, refurbished or destroyed. If returns are 10 to 30 percent of sales, the logic doesn’t suffice. In this case, one is forced to ship the returns to the distribution center and process them there, or seek an alternate solution.
There are goods firms that have a 5 per cent returns clause with their distributors that the latter shall not be liable to take back more than 5 per cent of the goods returned by the customer. The onus of managing the stock of the leftover goods returned is on the eCommerce platform again which in turn, has to auction the products at a discounted rate.
For instance, Raul Castilla, director of reverse logistics at Wal-Mart, mentions that each year, the firm processes 45 million cases of returned merchandise through its regional return centers in the form of returns, refurbishments and disposals.
In addition to the existing overheads of managing and optimizing the cost of returned goods, there are other issues that contribute to the irrational difficulty in handling reverse logistics. The chief amongst them being lack of fair quality checks & standardization in weights and volumes. Products, when dispatched to customers are packaged well. However, during returns, items may come back with or without packaging, thus resulting in inconsistent packing volumes and unforeseen damages during transportation. Efficient inventory management for returned goods becomes a humongous task to handle over time. Another evil that one may come across in the retail industry is a rise in return fraud.
Apart from this, institutional pressures from the government, customers, and competitors play an important role in determining a firm’s stand on effective implementation of reverse logistics. At times, factors governing a sales slump may not be attributed to the product itself. The inability to handle rejected goods because of packaging/transporting deficiencies usually leads to decline in sales. It also gives rise to increased returns’ costs and inefficient order fulfilment.
We have come across instances where the average returns for products shipped back have soared to as high as a quarter of the gross value booked initially. Returns have been highest in apparel, mobile and electronics categories.
Reverse Logistics Challenges, such as these, do not simply go away. Unfortunately, customers do!
As Jian Xu commented in “Study of Reverse Logistics in the eCommerce Environment” — “The lack of good return channels is the main reason for the customers to give up on-line transactions. Many well-known companies take reverse logistics strategy as an important tool to reduce costs, increase customer satisfaction and strengthen the competitive advantage. As a result, eCommerce development cannot leave the support of reverse logistics and the efficient operation of the reverse logistics also need eCommerce.”
To be competitive in today’s marketplace, reverse logistics has to be looked at as an entity directly linked to consistency in profit or loss. Planning and optimizing on demand and scheduled dispatches /returns works wonders. Adhering to SLAs is the key to attain sustainability in the market and improve customer satisfaction. Being able to address environmental concerns regarding safe disposal/recycling of rejected goods as in the case of batteries, air conditioners is a cause worth being prioritized.
Distribution systems are one of the most effective parts of the supply chain network and the total costs incurred heavily depend on transport. Vehicle Routing Problem (VRP) is an effective issue in reverse logistics and closed loop supply chains. Solutions in the form of efficient dispatch planning, route optimization and fleet management allow firms not only in getting things right in the first go but also provides them with a leverage to improve and make mid-course adjustments. Another aspect here is clubbing an on-demand pick up with an existing scheduled beat. For instance, issuing a pickup order for an exchange offer on the fly where the rider was initially supposed to just drop a mobile phone at the customer’s location. This amalgamation of scheduled and on-demand orders gives the operations team more control and better visibility of their fleet.
Availability of structured data about the returns in a particular season or festivity directly impacts the forward planning for the next.
With growing customer expectations and new retailers entering the market, there is a constant battle to cut costs and enhance customer experience. Handling returns effectively, is a game changer here.
At Locus, we add intelligence to logistics and aim to automate decisions. Our platform lets our clients automagically plan & optimize their on-demand & scheduled deliveries/pick-ups keeping in mind several business parameters such as SLAs, live traffic density etc. With the entire fleet being tracked live at all times, addressing on ground issues real-time, becomes a breeze.
Even in handling reverse pick-ups, Locus’ logistics platform provides our clients features to take into account, nuances like the volume and fragility of the product being returned. The returned product can be stacked in perfectly considering the LIFO logic and hence the repacked volume is optimized. Additionally, the routing engine works efficiently even if an order comes in after the fleet has been mobilised by pushing it to the most optimal route thereby maintaining efficient clustering and compactness of geo clusters. Needless to say, the distance and time on road in these cases is dynamically optimized.
And what does data say?
- 8% increase in the number of customers now served within SLAs for on-demand operations.
- 25% increase in operational efficiency and decrease in operational costs.
- 100% increase in the number of orders done per vehicle for intracity C2C deliveries.
So the next time you think Logistics, forward or reverse, think Locus.
Like what you read? Reach out to us at contact@locus.sh


Related Tags:
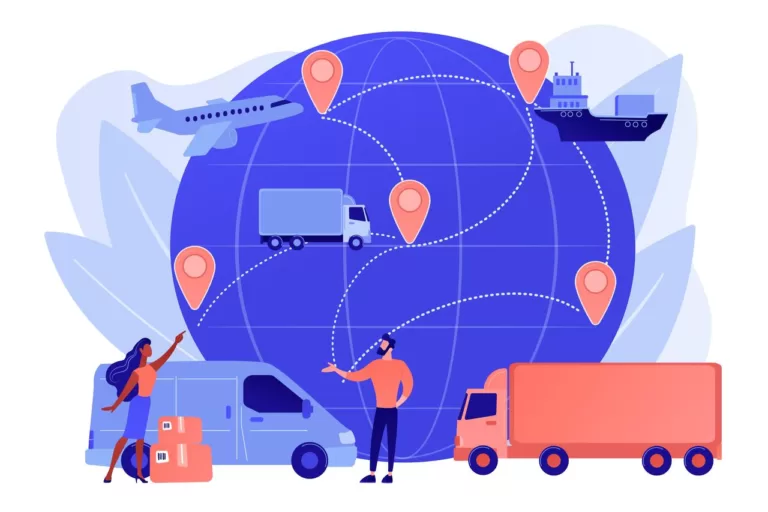
Route Optimization
How good is your Geocoder?
What is the purpose of geocoding? Geocoding is a very important piece of the intricate logistics puzzle that Locus is solving for its clients. This merits a constant evaluation of its performance over different regions of the world. However, getting a sense of how good a geocoder is performing requires a very nuanced selection of the metrics […]
Read more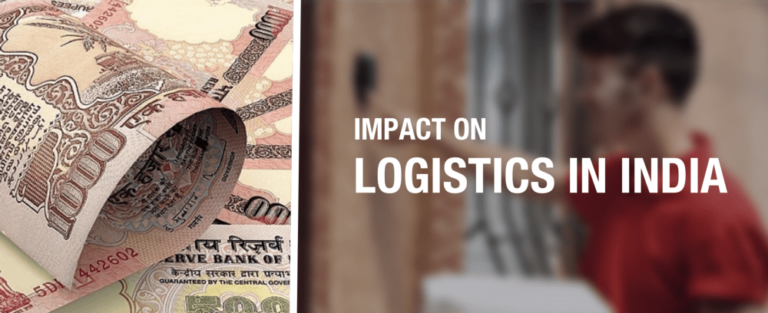
Fleet Optimization
Effects of Demonetisation on Logistics Sector – Boon Or Bane
Demonetisation of 500 and 1000 Rupee notes- Boon Or Bane for the Logistics Sector? While the western side of the world is undergoing a major political sea change, India has been stumped by a surprise currency ban. Indians struggled to pay for basic goods like food and fuel yesterday and fretted about their savings, after […]
Read moreMOST POPULAR
EDITOR’S PICKS
SUBSCRIBE TO OUR NEWSLETTER
Stay up to date with the latest marketing, sales, and service tips and news
Reverse Logistics : Forward Thinking Pays Big Dividends